What is Sheet metal stamping process?
The process of turning sheet metal into useful parts or components is called sheet metal stamping. The metal is fed into a press in which the stamping tool (also called a die) forms the desired shape. A mold is pressed into or through metal with great force. The force used in this process is in tons.
Except for some special processes, sheet metal stamping does not use heat. Instead, it is done by cold forming technology. Even if no heat is used, the parts will become hot due to the friction between the metal and the mold caused by the force of the press.
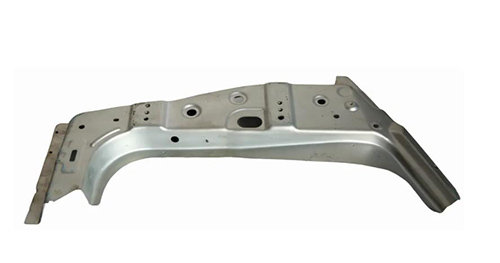
Sheet metal parts
Common sheet metal stamping process
There are basically only three components of sheet metal stamping – sheet metal, dies, and presses – but any single part may require multiple steps to reach its final shape. The following guidelines explain some common processes that can occur during metal stamping.
- Forming: Forming describes the process of transforming a flat metal into another shape by applying force. It can be done in one of several ways, depending on the design specification of the part. Through a series of operations, metals can change from relatively simple shapes to complex shapes.
- Blanking: blanking is the most basic technology. When the sheet or blank is fed into the punch, the punch will cut the required shape in the punch. The resulting work is called blank. A blank may be a required part, also known as a fully completed blank, or it may continue with subsequent forming steps.
- Drawing: Drawing is a more complex operation, which is the formation of blood vessels or deep depressions. Tension is used to carefully pull the material into the cavity to change its shape. Although the material may stretch during stretching, the technician will try to avoid stretching to keep the material intact. The sinks, cookers, oil pans, etc. used for cars are usually made of wire drawing.
- Piercing: Piercing is almost the opposite of blanking, but the technician does not keep the blank, but uses the material around the outside of the punching area. For example, think of cutting cookies from a round dough. During blanking, biscuits are saved; On the other hand, in the process of perforation, biscuits will be discarded, and the residue with holes is the ideal result.
Material Science
Although almost any metal (including gold) can be stamped, sheet metal is by far the most common. The type of metal used depends on the type of part required and its required characteristics, such as corrosion resistance and heat resistance.
Sheet metal stamping can produce parts with the following materials:
- stainless steel
- Mild steel and high carbon steel
- aluminium
- titanium
- brass
- bronze
- copper
- Inconel
- Nickel alloy
Application of Sheet Metal Stamping
In the stamping process, highly specialized computer aided drawing and manufacturing programs are used to process sheet metal into complex parts. Sheet metal stamping can quickly and efficiently produce high-quality, flexible heavy parts. The results are very accurate and generally more reliable and consistent than manual machining.
The following industries use components created by sheet metal stamping:
- automobile
- renewable energy
- Medical
- Industrial
- space flight
- Hardware
- home decoration
This list is by no means exhaustive. The demand for sheet metal stamping is large, and the industry relying on it is wide.
Precision sheet metal stamping service
When your industry needs high-quality precision parts, you need a stamping company that meets the most stringent quality standards. ZenaTech is a company registered in ISO 9001:2015 and has been manufacturing precision tools for companies around the world since 1990. Today, we produce more than 1 million highly refined parts every week, even for the most technologically advanced applications.
To learn more about our stamping service, please visit our service page or ask for a quote online. If you have any questions, please contact ZenaTech. immediately.