Metal stamping die burst is a very common phenomenon, the general metal stamping die will only burst a small gap, but serious, stamping die may crack into several pieces of broken plate, metal stamping die burst there are many reasons, die design, manufacturing materials, metal stamping processing technology and other factors may affect the quality of the die.
Cause analysis of metal stamping die burst
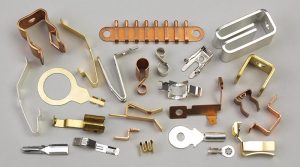
Stamping Part ,Stamping Parts Manufacturer
Reasons for the design of metal stamping die.
Generally speaking, if the structure of the metal stamping die is not reasonable in design, the strength is not enough, the distance between the knife edge is too close, the number of template blocks is not enough or there is no pad, then the die is faced with a great risk of explosion. Mold design mainly includes the following points.
- Layout and edging: reciprocating feeding layout often causes damage to the die. If the edge value is too small, it will also aggravate the wear degree of the stamping die. Therefore, choosing a reasonable layout method and edging value can prolong the service life of the die and avoid bursting.
- Accuracy of guiding mechanism: accurate and reliable guiding, can reduce mold wear, avoid concave and convex die gnawing. Especially suitable for no gap, small gap punching die, compound die, multi – station progressive die. In addition, in order to improve the life of the die, it is also necessary to choose the correct guiding form and guiding mechanism precision according to the nature of the processing technology and the precision of the die parts.
Reasons for metal stamping processing technology.
It has been proved that the hot working quality of metal stamping die has great influence on its performance and service life. According to the analysis and statistics of die failure causes, die failure “accidents” caused by improper heat treatment account for more than 40%. In the process of making metal stamping die, improper conditioning process will cause deformation of the finished product and eventually lead to cracking of the metal stamping die.
- Preliminary heat treatment: According to different die materials and requirements, operators need to adopt annealing, normalizing or tempering and other preliminary heat treatment, in order to eliminate the structural defects of forging blanks and improve the level of processing technology. In addition, proper preliminary heat treatment of die raw materials can make the carbide distribution more uniform, which is beneficial to ensure the quality of conditioning and prolong the life of the die.
- Conditioning: This is the key link of mold heat treatment. If the temperature in the quenching process is too high, it will lead to brittleness of the mold, and the products produced are easy to deformation and fracture in the cooling process, which seriously affects the service life of the mold. In the process of die quenching heating, the operator should strictly abide by the process specification of heat treatment, especially pay attention to the occurrence of oxidation and decarburization. If conditions permit, vacuum heat treatment can be used. In addition, quenching should be timely tempered, and according to the technical requirements of different tempering process.