Springs Type.
There are tension spring, compression spring, torsion spring and bending spring. According to the shape, there are disc spring, ring spring, plate spring, spiral spring, truncated cone scroll spring and torsion bar spring. In production process, there are cold coil spring and hot coil spring.
Springs Material.
The common cylindrical spring is normal because of its simple manufacture and simple structure. Generally speaking, spring materials should have high elastic limit, fatigue limit, impact toughness and good heat treatment performance. Carbon spring steel, alloy spring steel, stainless spring steel, copper alloy, nickel alloy and rubber are normal material.
The manufacturing methods of spring include cold coil method and hot coil method. The diameter of spring wire less than 8 mm is generally cold coiling, and that larger than 8 mm is hot coiling. Some springs need to be pressed or shot peened after being made, which can improve the bearing capacity of springs.
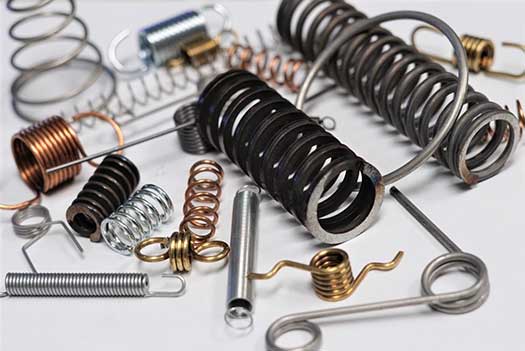
custom springs in custom compression spring, torsion spring, extension spring
There are 6 categores Springs:
1. Torsion spring.
It is a kind of spring which bears torsion deformation. Its working part is also tightly wound into a spiral shape. The end structure of torsion spring is processed into various shapes of torsion arm, not hook ring. Using the lever principle, torsion spring has great mechanical energy by twisting or rotating the elastic material with soft material and high toughness.
2. Tension spring.
It is a spiral spring that bears axial tension. In the case of no load, the tension spring between the coils is generally tight and there is no gap.
3. Compression spring.
It is a spiral spring which bears axial pressure. Its material section is mostly circular, and it is also made of rectangular and multi strand steel. Generally, the spring is of equal pitch. The shape of compression spring is cylindrical, conical, convex and concave, and a small amount of noncircular. There is a certain gap between the coils of the compression spring, which will spring when subjected to external load Spring shrinkage deformation, storage deformation energy.
4. Progressive spring.
This kind of spring adopts the design of inconsistent thickness and density. The advantage is that when the pressure is not large, it’s good. It can absorb the fluctuation of the road surface through the part with low elastic coefficient to ensure riding comfort. When the pressure increases to a certain extent, the thicker part of the spring plays the role of supporting the body. However, the disadvantages of this spring are that the handling feeling is not direct and the accuracy is poor.
5. Linear spring
Linear spring from top to bottom of the thickness, elastic coefficient is a fixed value. This kind of spring can make the vehicle obtain more stable and linear dynamic response, which is beneficial to the driver’s better control of the vehicle. It is mostly used for performance oriented modified vehicles and competitive vehicles, but the disadvantage is that the comfort is affected.
6. Compared with the original spring, the short spring is shorter and more robust.
The installation of short spring can effectively reduce the center of gravity of the vehicle body, reduce the roll generated during cornering, make the bending more stable and smooth, and improve the vehicle’s handling ability in the curve.
However, the damping setting of the original shock absorber tends to be comfortable, so the short spring and the original shock absorber are not very stable in matching. It can not effectively inhibit the rebound and compression of the short spring. When driving on the bumpy road, there will be an uncomfortable jumping feeling.
In the long run, the service life of the shock absorber will reduce. Of course, the above conditions are relatively speaking. There will not be such serious damage in daily driving, and try not to drive violently. After all, the original shock absorber can not bear the pressure of high load.
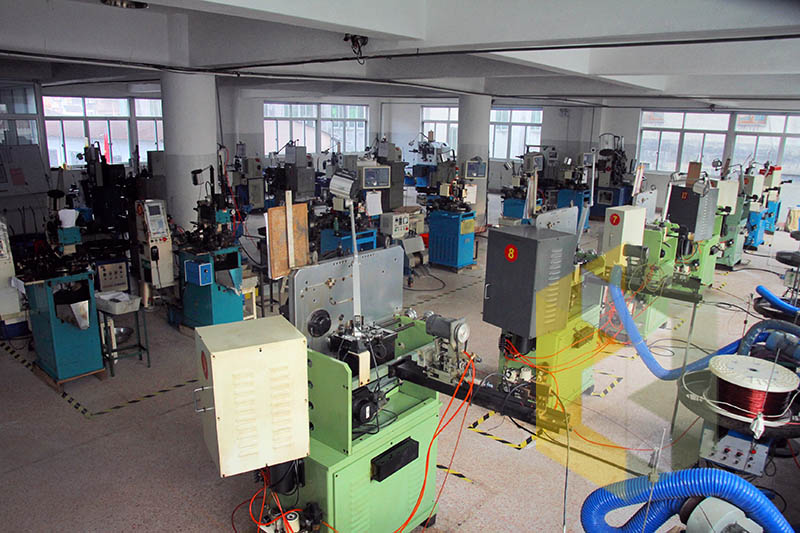
Spring Manufacturing technology
Cold forming
1) One time automation ability of cold forming process.
There are 12 claws in cold forming machine. 8-claw forming machine can make springs in steel wire in the range of (0.3-14) mm. The development direction of forming process equipment:
① to improve the forming speed, the main development trend is to improve the forming speed of equipment;
② to improve the durability of equipment by improving the fineness of equipment parts and strengthening the heat treatment effect;
③ adding length sensor and laser distance meter to stop the automatic closed-loop control manufacturing process for CNC forming machine.
2) The range of cold forming process is.
The spring coiler with large wire diameter has a maximum specification of 20 mm, = 2000 MPa and a winding ratio of 5. It’s still limited in the cold forming process of minic block spring and eccentric spring with variable diameter or equal diameter.
Thermoforming
1) The speed of hot forming process is very high.
In China, People use CNC 2 shaft hot coiling machine to form (9 ~ 25) mm specifications. The maximum speed is 17 pieces per minute. Compared with the prosperous countries, there is a big gap.
2) The technology control ability of large spring hot forming.
Because there is only CNC2 axis hot coiling spring machine, the shape control is less than three directions, and the precision is poor. There is no automatic bar rotation control and adjustment mechanism, so the forming process degree and ability of hot coil spring are low. Therefore, the accuracy of the spring and the surface oxidation decarburization degree are also low.
① Control mechanical movement.
Such as valve spring in internal combustion engine, control spring in clutch, etc.
② Absorb vibration and impact energy.
Such as buffer spring under car and train carriage, vibration absorption spring in coupling, etc.
③ Store and output energy as power.
Such as clocks, springs in guns, etc.
④ Force measuring element.
Such as the spring in the force measuring device and spring scale.
Spring stiffness is the ratio of load to deformation of spring. The greater the stiffness, the harder the spring. People use spring as elastic element widely in mechanical and electronic industries. When loaded, the spring can produce large elastic deformation and convert mechanical work or kinetic energy into deformation energy. After unloading, the deformation of spring disappears and returns to its original state.