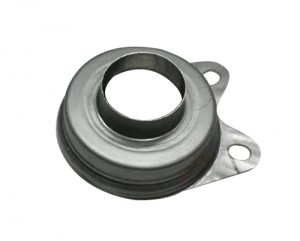
The following measures can be taken to prevent failures of the cutting head
I. In terms of equipment management:
- Regular maintenance: Formulate a strict equipment maintenance plan and conduct comprehensive inspections and maintenance of the cutting head regularly. This includes cleaning lenses, checking seals, and adjusting the optical path. For example, perform minor maintenance once a month to clean the dust and oil stains on the surface of the cutting head and check whether the nozzle is blocked; perform major maintenance once a quarter to deeply clean and calibrate the optical elements inside the cutting head.
- Quality monitoring: Monitor the working status of the cutting head in real time during equipment operation. Sensors can be installed to monitor parameters such as the temperature, pressure, and vibration of the cutting head. Once an abnormality is found, an alarm should be issued promptly and measures taken. For example, when the temperature of the cutting head is too high, automatically reduce the laser power or suspend cutting to prevent overheating and damage to the cutting head.
- Spare parts reserve: Reserve a certain number of spare parts for key components of the cutting head, such as lenses, nozzles, and seals. In this way, when a failure occurs, they can be replaced in time to reduce downtime. At the same time, ensure the quality and compatibility of spare parts to avoid more problems caused by using inferior spare part
II. In terms of operation specifications:
- Train operators: Provide professional training to operators to familiarize them with the working principle, operating procedures, and precautions of the cutting head. Operators should master the correct operation methods such as starting, stopping, and adjusting parameters to avoid cutting head failures caused by misoperation. For example, when replacing the lens, it must be carried out in strict accordance with the operating procedures to avoid lens contamination or damage.
- Standardize operation processes: Establish standardized operation processes and require operators to operate strictly in accordance with the processes. For example, before cutting, the plate must be cleaned to avoid impurities from entering the cutting head; during cutting, maintain a stable cutting speed and power to avoid sudden changes from impacting the cutting head.
- Safe operation: Emphasize the importance of safe operation and ensure that operators comply with safety regulations when operating the equipment. For example, wear personal protective equipment such as protective glasses and gloves to avoid laser damage to the human body; when the equipment is running, it is forbidden to open the cutting head protective cover to prevent accidents.
III. In terms of environmental control:
- Maintain a clean environment: Keep the environment around the cutting equipment clean to reduce the impact of dust, oil stains and other impurities on the cutting head. Air purification equipment can be installed and the work area can be cleaned regularly to ensure good air quality. For example, clean the work area every day and use a vacuum cleaner to clean the dust on the ground and the surface of the equipment.
- Control temperature and humidity: Ensure that the temperature and humidity of the working environment are within an appropriate range. Excessive temperature and humidity may affect the performance and service life of the cutting head and even lead to failures. Equipment such as air conditioners and dehumidifiers can be installed to adjust the environmental temperature and humidity. For example, control the working environment temperature at 20-25°C and the humidity at 40%-60%.
- Prevent vibration and shock: Install the cutting equipment on a stable workbench to avoid vibration and shock. Shock-absorbing pads, anchor bolts and other fixtures can be used to reduce the impact of external vibrations on the cutting head. For example, when installing the equipment, choose a sturdy workbench and use shock-absorbing pads to reduce vibration transmission.